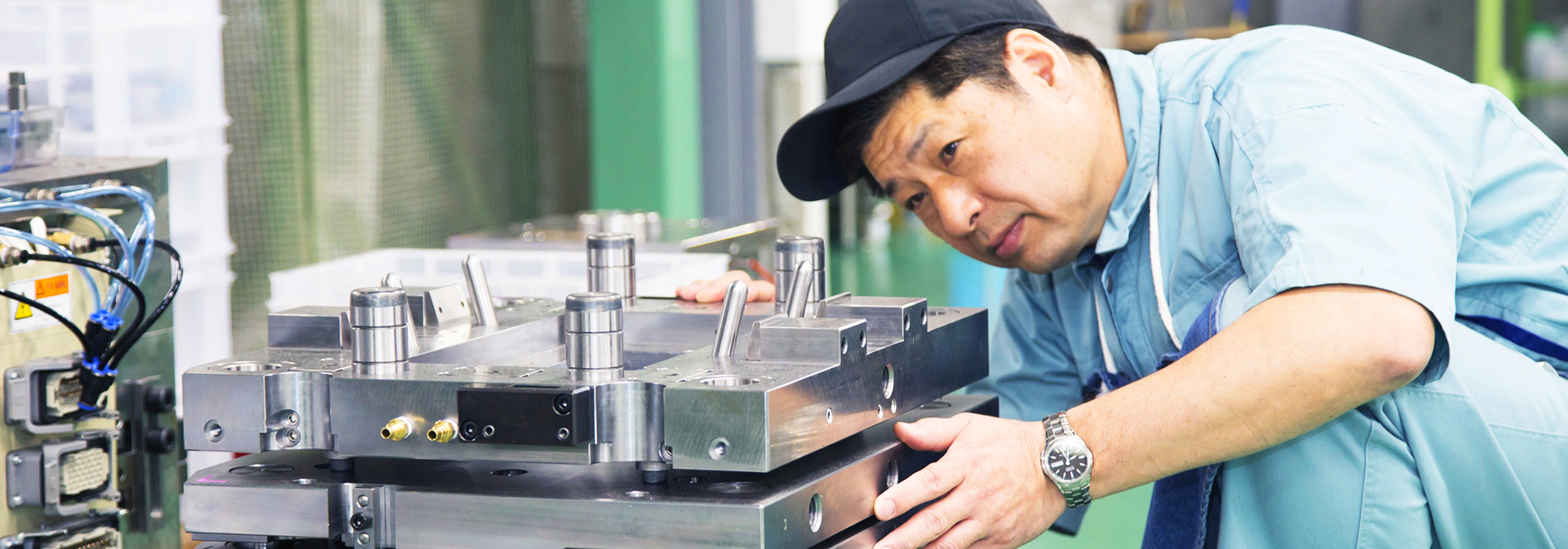
We consider die structure to minimize defects expected in mass-production from the stage of prototype dies, and utilize our design ability and die processing technologies we have cultivated over the years to design, manufacture, and assemble high quality injection molding dies and stamping dies.
We conduct prior verification such as resin fluid analysis for mold conditions such as the gate position, resin injection pressure and filling time, and die temperature. We then determine the die structure upon comprehensively investigating the specifications, drawing requirements, and product shape received from the customer. The molding conditions are determined based on resin properties obtained in production history and past launch data such as resin fluidity, gas position and volume, and rate of contraction.
Our molded products are produced from simple prototype dies according to customer evaluation and development steps.
We start by checking the dimensions of the prototype, then check for internal defects such as voids and external problems such as glass fibers, short shots, sink marks, burning, and flash, which may occur due to the resin material/product shape.
When performing die adjustment or changing conditions according to changes in the customer specifications, we are able to perform trial molding at our factory, which means that the new specifications can be quickly reflected in the molded product. We can then provide feedback on the status of product improvement.
As customer assembly processes become more automated and higher precision is required for component units, we identify concerns before mass-production drawings/mass-production dies and conduct adequate prototype evaluations.
With 3D scanner CMM from Keyence Corporation, we compare molded products at the prototype stage and CAD data with images to check for deviation and differences from the drawings. We also have coordinate measuring machines and Measuring microscopes, etc. measuring microscopes are also installed in our die manufacturing sites for on-the-spot checks.
The inspection jigs and tools used at our manufacturing sites are designed and produced in-house.
We confirm that metal stamped inserts are non-faulty within the process, and if there is any indication of a fault such as deformation, we quickly identify and deal with it.
We manage the maintenance and repairs conducted according to the maintenance frequency decided for the shot count and the design and production history of injection molding dies and stamping dies as "die records." Our technicians that are well-versed in both injection molding dies and stamping dies maintain quality on a daily basis. Should a problem happen to occur, they can check the die records to go through the past history and changes.