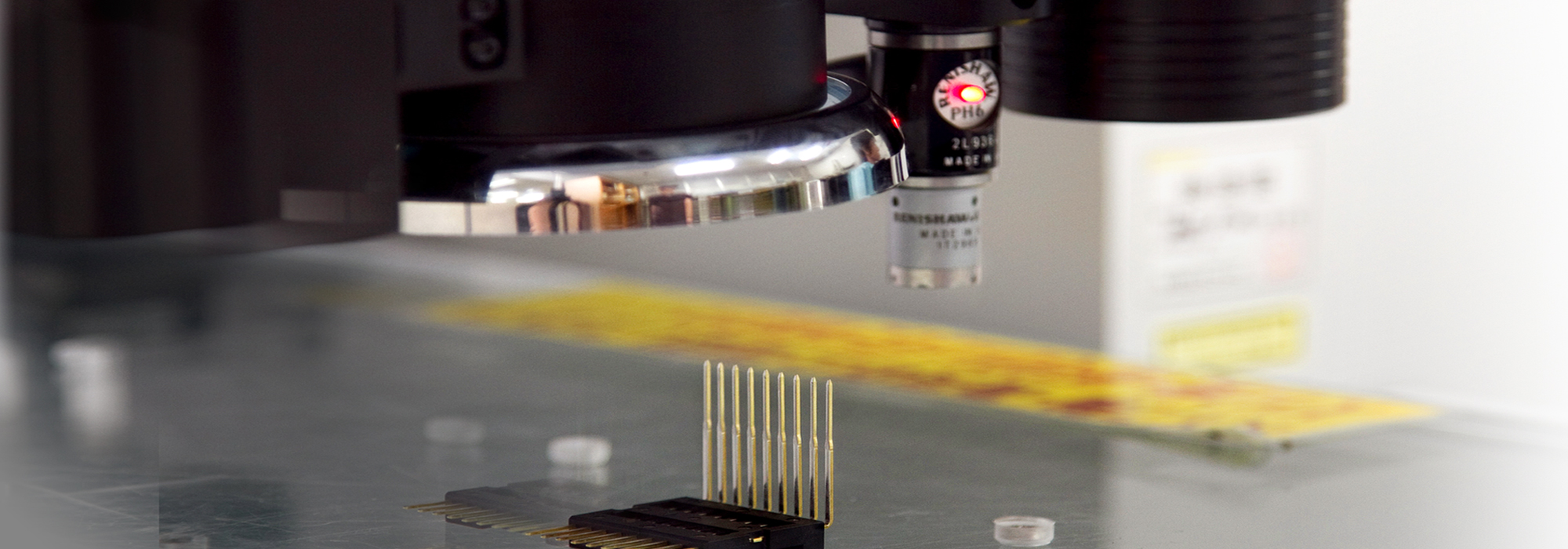
We have various inspection systems in order to respond to a wide range of inspections, such as dimensional measurement, whose requirements are getting stricter by the year, as well as micron-level evaluation, and image measurement of shapes that are difficult to measure, chamfers, and radiuses. We also have X-ray/CT scan equipment that can check the inside of resin, and can handle evaluations that influence the decisions made regarding specifications.
Furthermore, in regard to functional assurance other than dimensional measurement, we also have a wide range of experience with electrical testing and leak testing. When required, we can conduct external visual inspections and image judgment on all the items inside a process.
Dimension measuring devices such as coordinate measuring machines
Sub-micron level measurement microscopes
3D Scanner CMM
X-ray/CT scan equipment for non-destructive inspection inside components
Image Dimension Measuring System
Height and flatness measuring machine
Digital Microscope
Leak testing
We automate various types of electrical tests and incorporate them in automatic molding and hoop insertion processes.
In order to eliminate mistakes in manual tasks as much as possible, we capture and check the position and existence of metal stamped inserts with a monitoring camera.
We check the allowed horizontal position tolerance and height tolerance for terminals, which are delicate metal stamped inserts.
We perform electrical tests, external inspections, and leak tests with automated lines according to functional requirements.
Although faulty products are becoming less common due to the automation of manufacturing process and the adoption of cameras and sensors, when the external appearance has strict requirements, we perform visual inspections upon confirming the location and inspection conditions with the customer in advance.
We make efforts to understand detailed customer specifications and assembly line assembly methods not indicated in drawings and design and manufacture measurement jigs in-house.
Depending on the project, we consider the appropriate dimensional assurance method in coordination with the customer to preempt problems such as assembly not being possible on-site despite the molded products being made according to specification.
We store all information regarding our production status, plant temperature and humidity, and on-duty personnel as digital data. The entire flow is then understood and shared in order to create better manufacturing processes.
On the other hand, when variation or injection molding problems occur between mold lots, we quickly detect and respond to them. This enables us to utilize the data as evidence for identifying the cause of any possible problems.
We manage evidence of process capability indices, injection molding condition history, and documents created when mass-production is launched, as well as initial production control and change management after moving to mass-production.
We have completed construction of a clean room at our new Kanayama Plant (in 2019).
This has enabled us to create an environment free from the intrusion of contaminants as well as an inspection system with image detection.
We maintain a thorough management system for in-process and pre-shipping quality control according to ISO standards.
Furthermore, we have a particularly strict management system for dies that affect product quality, which makes decisions according to the shot count of each die and performs periodic maintenance. We call this system our hospital as it also handles repairs when a die is damaged.
■Environmental policy
As we manufacture resin products and dies, we aim to be a company that is friendly to the environment and in harmony with the local region, based on the principle of contributing to society.
We also conduct environment conservation management in order to save resources, save energy, and ensure corporate activities that consider the fact that the region is blessed by nature and a lush green environment.
■Quality policy
We will manufacture and supply products that our customers can rely on through the construction and complete functioning of a quality system that enables us to provide our customers with the maximum satisfaction.
■Applicable range
This applies to all environmental aspects that we specify as things that we can influence, things we can manage, and all the quality assurance work of the products and services that we manufacture.
Furthermore, the products we manufacture are divided into the following major categories.
1.Design and production of stamping dies and injection molding dies
2.Stamping processing, injection molding processing, and assembly of processed parts
Applicable sites:1491-1 Arima-cho, Kumano City, Mie Prefecture, 519-4325, Japan