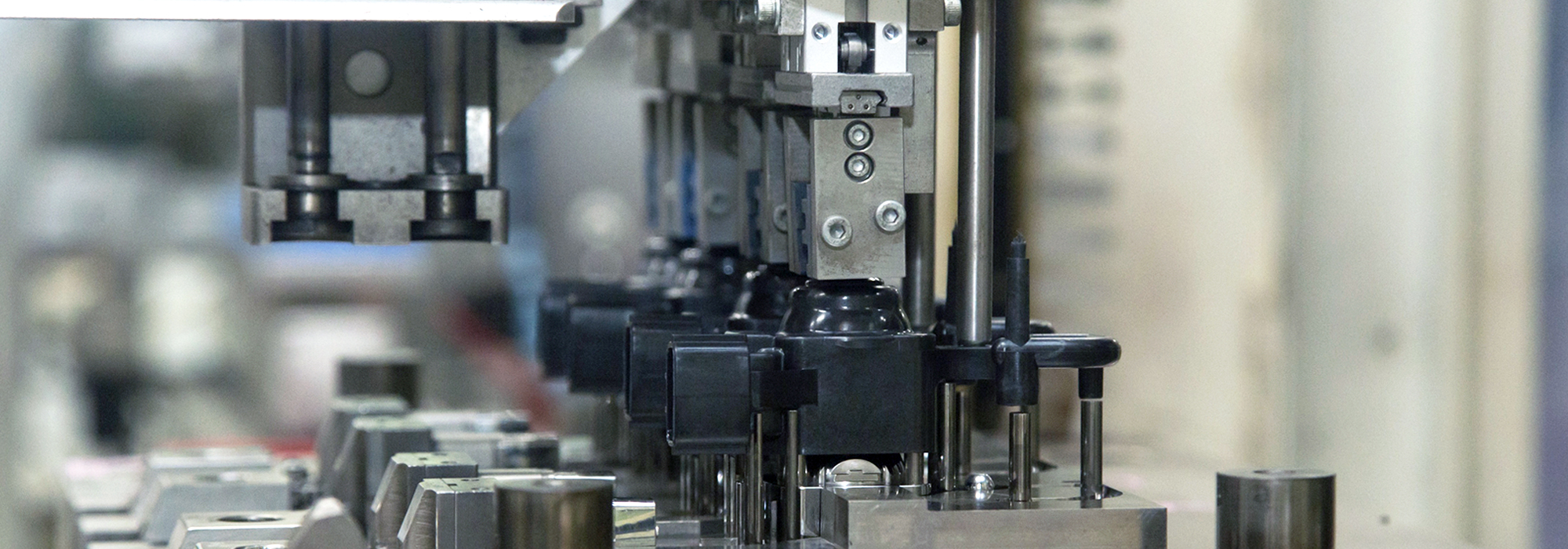
We focus on vehicle-mounted components, of which 60% are insert molded and 30% are injection molded. We also have a large number of vertical molding machines suitable for numerous metal stamped inserts and small lot/high variety products, as well as rotary injection molding machines that enable reduced preparation time and provide mass-production with efficient loading of multiple terminals.
Vertical molding machines (35 to 150 tons)
Horizontal molding machines (40 to 180 tons)
Vertical rotary injection molding machines (35 to 220 tons)
In addition to the method for inserting metal stamped inserts into dies manually or using a robot, we have also developed an in-house method for inserting a coiled metal material into the line then separating the pressed item after molding (hoop molding method). Installing sensors and cameras has also enabled us to build automated molding lines that can operate a maximum of 24 hours a day without human intervention.
Furthermore, we have developed technology for manufacturing a single coil by supplying two metal materials (coil materials) and joining them in the stamping process. Hoop molding achieves more stable production and saves labor and human resources.
In order to maintain the quality of insert molded products, the precision of the inserted component units (metal stamped inserts) is important. In order to ensure this important precision, we both design and manufacture stamping dies in-house and utilize them for the integrated manufacturing of metal stamped inserts. This enables us to maintain quality via complete in-house production.
We have hydraulic/high-speed presses, mechanical presses, and AC servo presses.
Press machines (10 to 300 tons)
Our 300 ton press machines are the latest equipment adopted in July 2019.
We can ship products that are semi-assembled in order to make them easier to assemble at the customer site, according to specifications and requirements.
For tasks that do not need to be performed manually, we also have experience with automated assembly, such as primary locking of waterproof rubber to the retainer of connector components and tightening of screws and fitting capacitors to molded products.